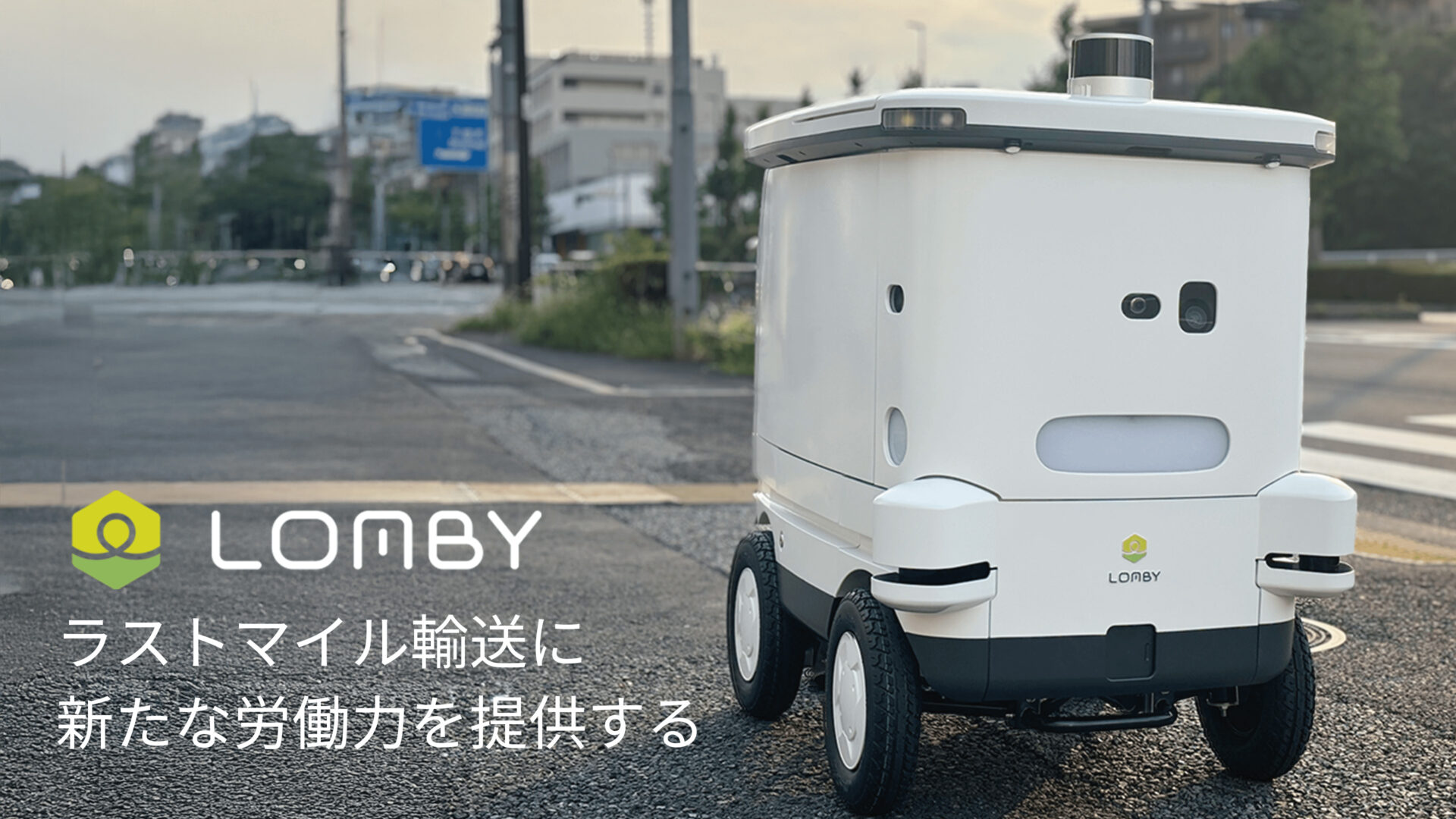
SERVICE
Autonomous Delivery Robots Support Local Communities Facing Labor Shortages
Autonomous Delivery Robots Support Local Communities Facing Labor Shortages
As Japan faces a super-aging society due to declining birthrates and a growing elderly population, labor shortages have become an increasingly serious social issue.
To address these challenges, autonomous delivery robots developed in Japan are stepping in to handle short-distance package deliveries and assist with personal mobility.
They aim to establish a new social infrastructure that supports daily life and contributes to a future where humans and robots work together.
By embracing this technology, we take a step toward a more sustainable society.
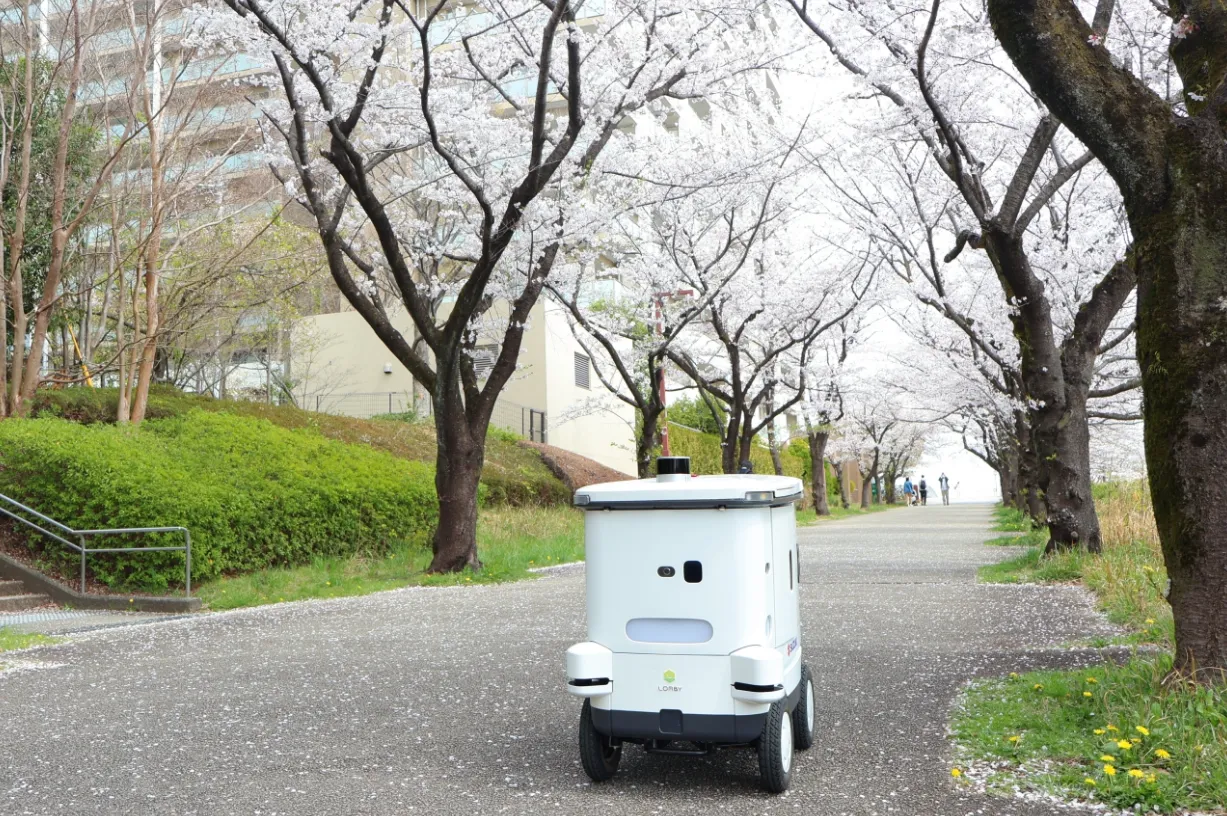
As Japan faces a super-aging society due to declining birthrates and a growing elderly population, labor shortages have become an increasingly serious social issue.
To address these challenges, autonomous delivery robots developed in Japan are stepping in to handle short-distance package deliveries and assist with personal mobility.
They aim to establish a new social infrastructure that supports daily life and contributes to a future where humans and robots work together.
By embracing this technology, we take a step toward a more sustainable society.
-Features of LOMBY
Reliable, Efficient, and Cutting-Edge — An Evolved Last-Mile Solution
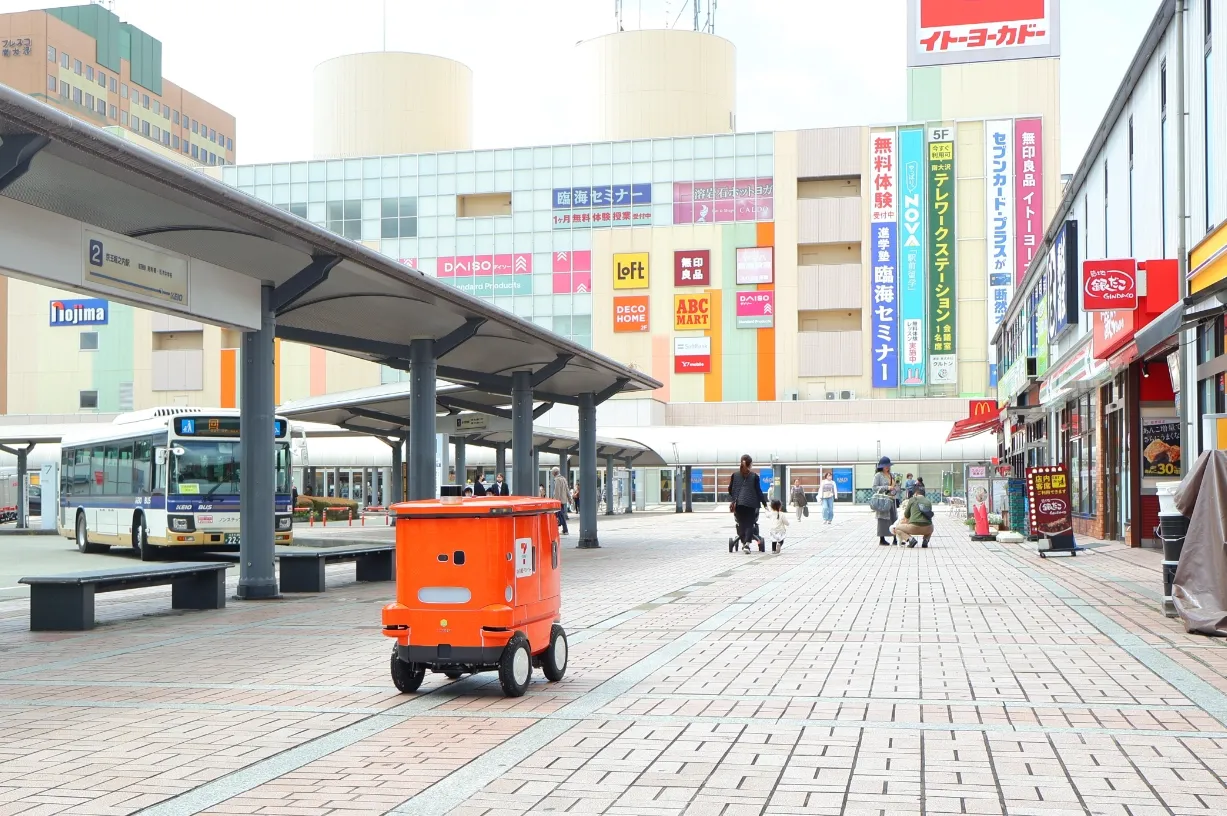
Expand Your Reach Within a 2–3km Radius of Your Store
LOMBY’s autonomous delivery robots travel on sidewalks at a maximum speed of 6 km/h, making them ideal for deliveries within a 2–3 km radius from retail locations.
For businesses whose target customers reside within this area, LOMBY provides an effective way to expand service coverage.
By building a flexible and sustainable delivery network, companies can tap into new customer segments and create new revenue opportunities.
A Practical Solution to Labor Shortages
In an aging society facing severe labor shortages, LOMBY is gaining attention as a “new labor force” that can replace human workers.
One of LOMBY’s key advantages is its ability to maintain stable last-mile delivery operations even in areas where staffing is difficult.
By covering the final mile from stores or logistics hubs, LOMBY not only reduces operational burdens for businesses but also serves as a convenient and dependable local infrastructure for residents.
Implementing LOMBY supports both the resolution of social issues and the development of a more sustainable lifestyle foundation.
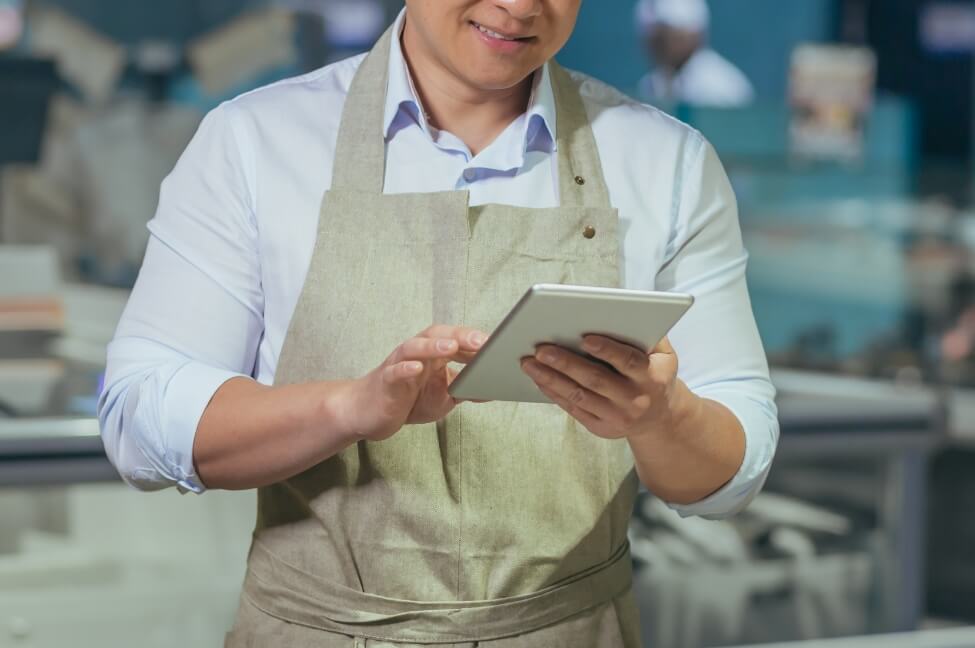
A Practical Solution to Labor Shortages
In an aging society facing severe labor shortages, LOMBY is gaining attention as a “new labor force” that can replace human workers.
One of LOMBY’s key advantages is its ability to maintain stable last-mile delivery operations even in areas where staffing is difficult.
By covering the final mile from stores or logistics hubs, LOMBY not only reduces operational burdens for businesses but also serves as a convenient and dependable local infrastructure for residents.
Implementing LOMBY supports both the resolution of social issues and the development of a more sustainable lifestyle foundation.
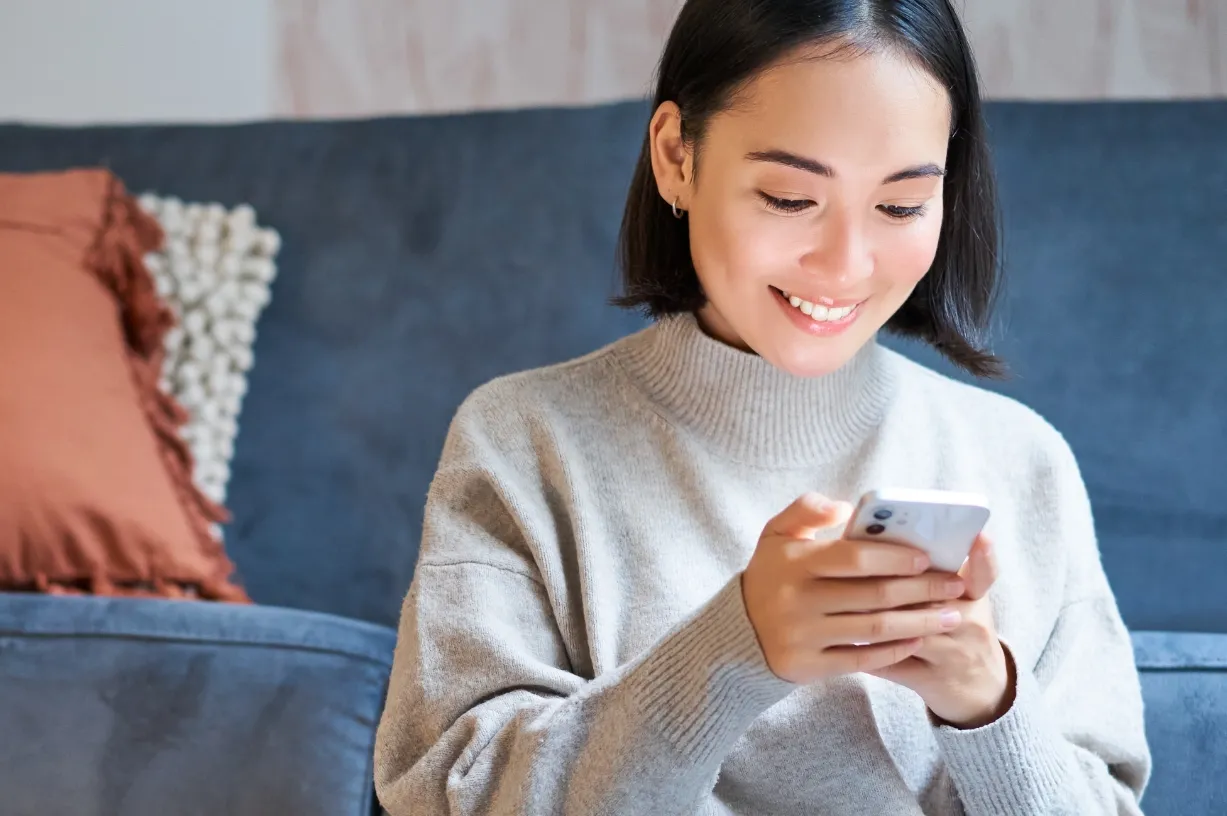
Seamless Integration with Existing Apps and Web Services
LOMBY can be integrated with third-party smartphone apps and web services, allowing items purchased through those platforms to be delivered by robot.
When robot delivery is offered as a selectable delivery option, it enables a smoother and more seamless user experience.
-What LOMBY Can Do
More freedom and kindness in both delivery and transportation.
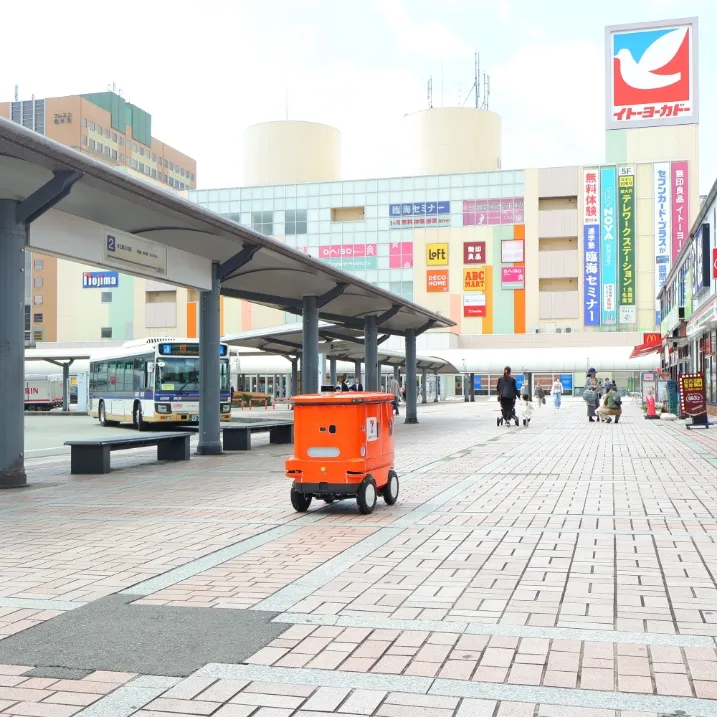
Unmanned delivery from stores
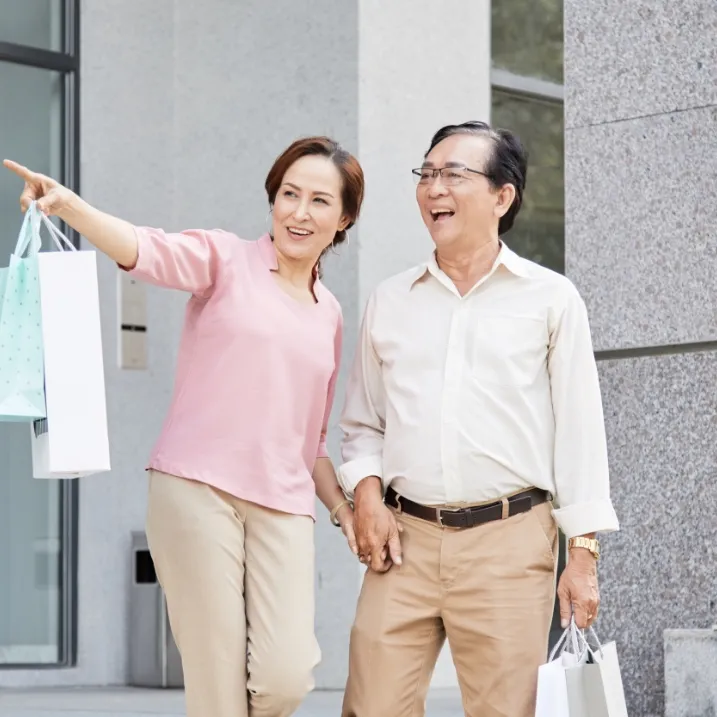
Transport support for elderly people and shoppers
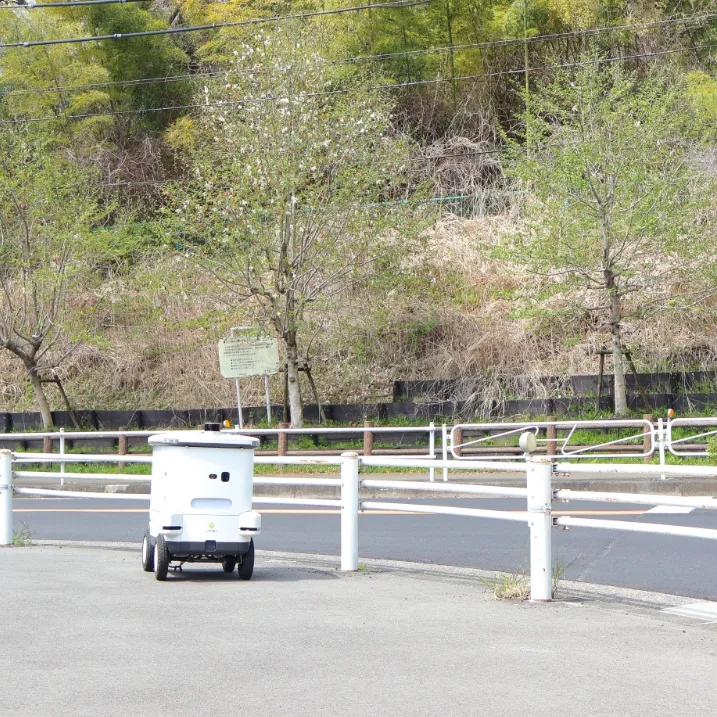
Applicable in various environments such as residential areas, suburbs, and inside facilities
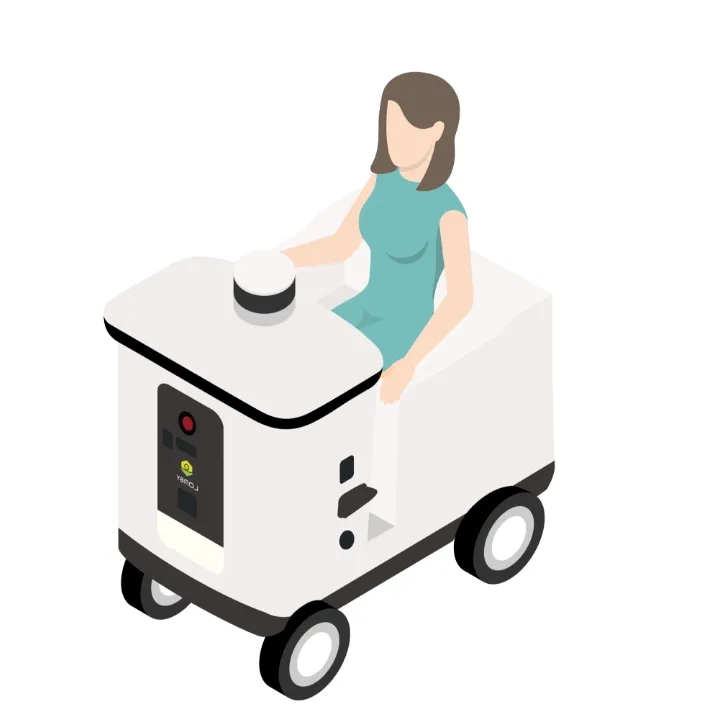
Planned expansion into personal mobility with “LM-P”
Benefits of Implementation
Achieve both labor-saving and high service quality while keeping costs low
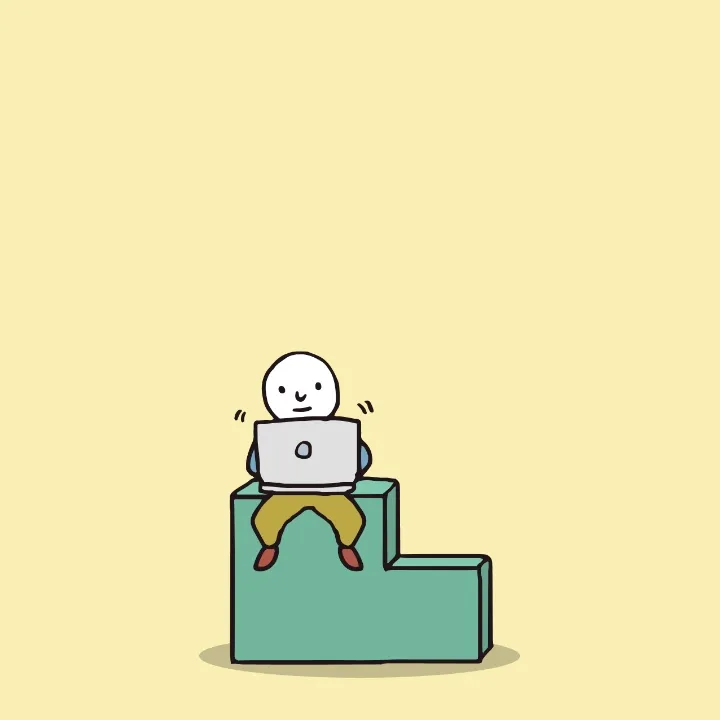
No need to station personnel on-site
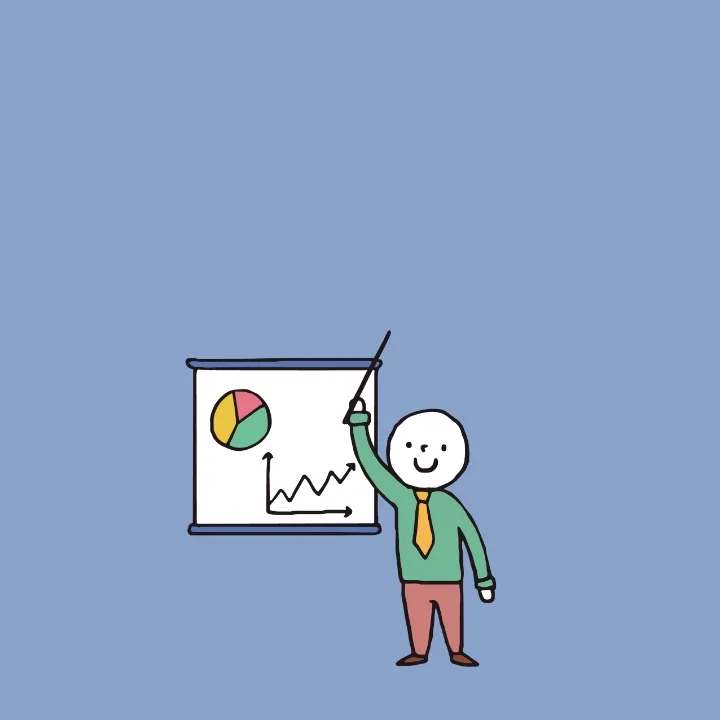
Delivery costs are less than half compared to manual labor
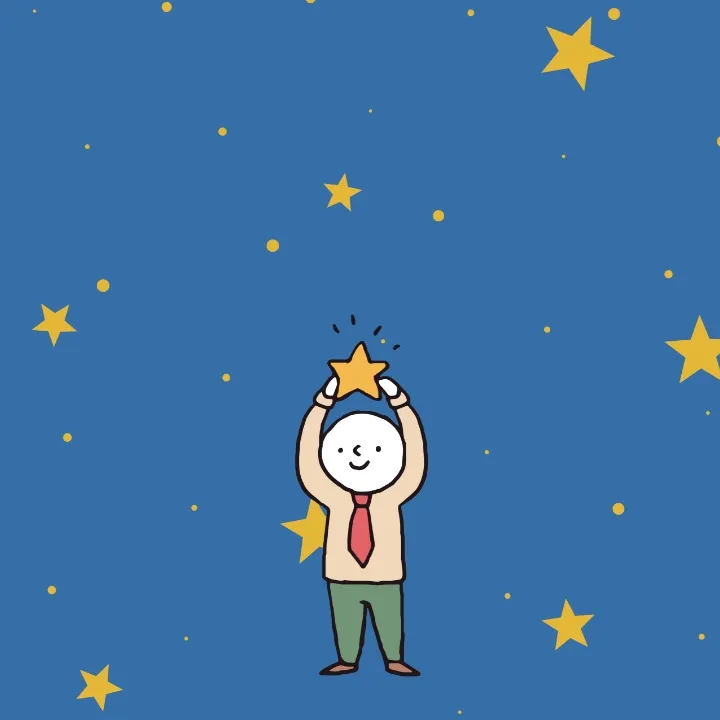
Operates even in rainy weather or at night, ensuring stable service
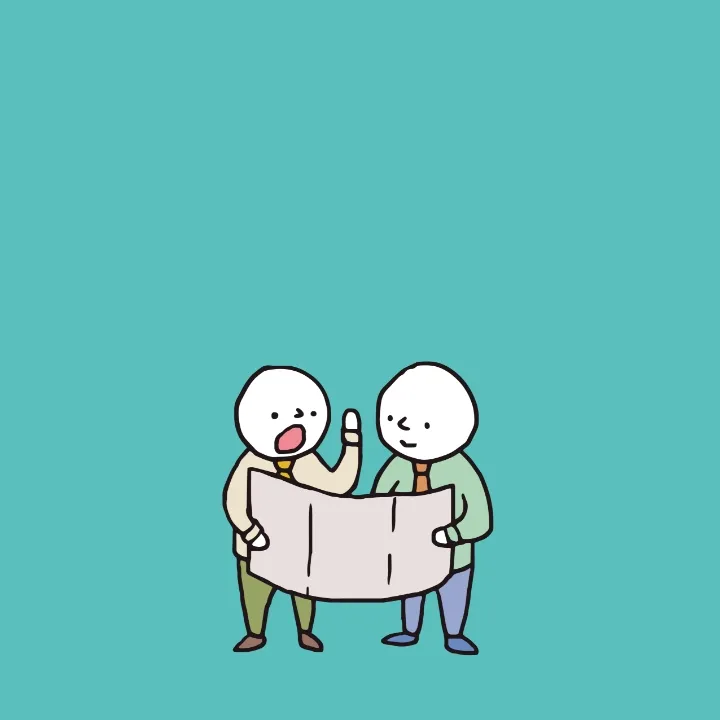
Effective for expanding market reach in rural and suburban areas
Proof of Concept and Partnerships
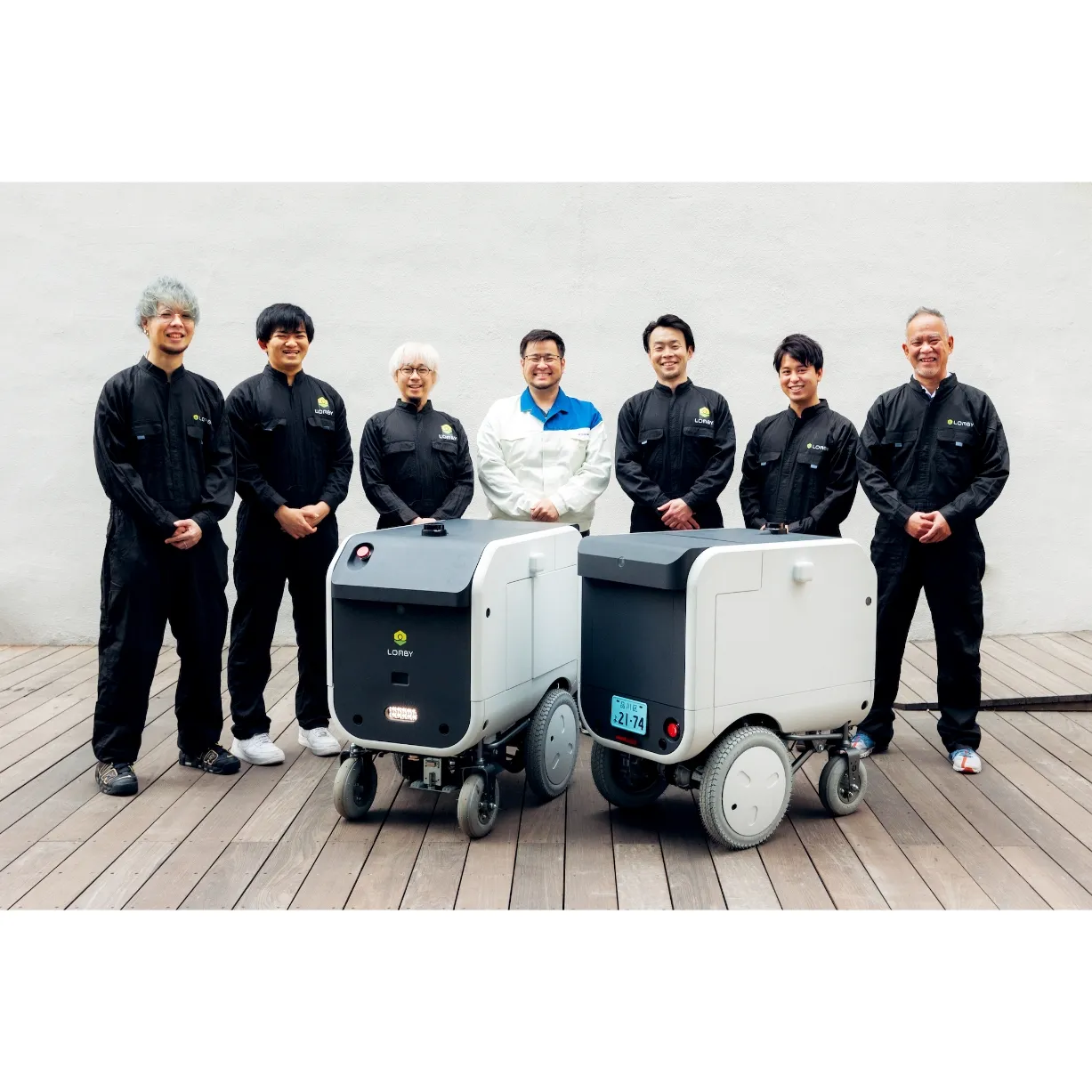
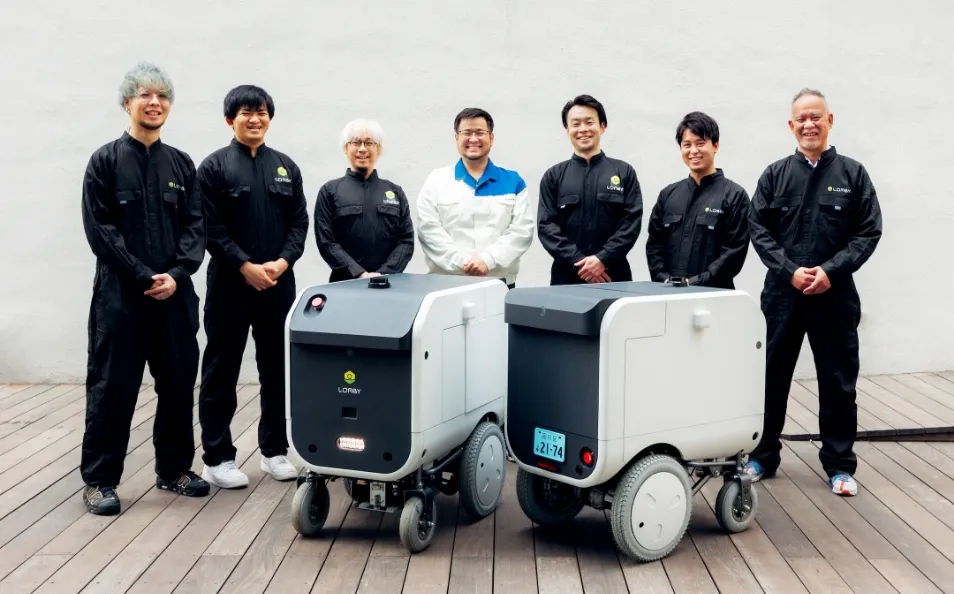
Achieving High Durability and Mass Production Through Collaboration with Suzuki
LOMBY has partnered with Suzuki Motor Corporation to jointly develop a design that balances the high durability required in real-world operations with the scalability needed for mass production.
The robot is engineered to meet the robustness and long operational hours expected of autonomous delivery units, while also considering a production framework capable of supporting large-scale deployment in the future.
This partnership enables consistent product quality, even during mass production phases.
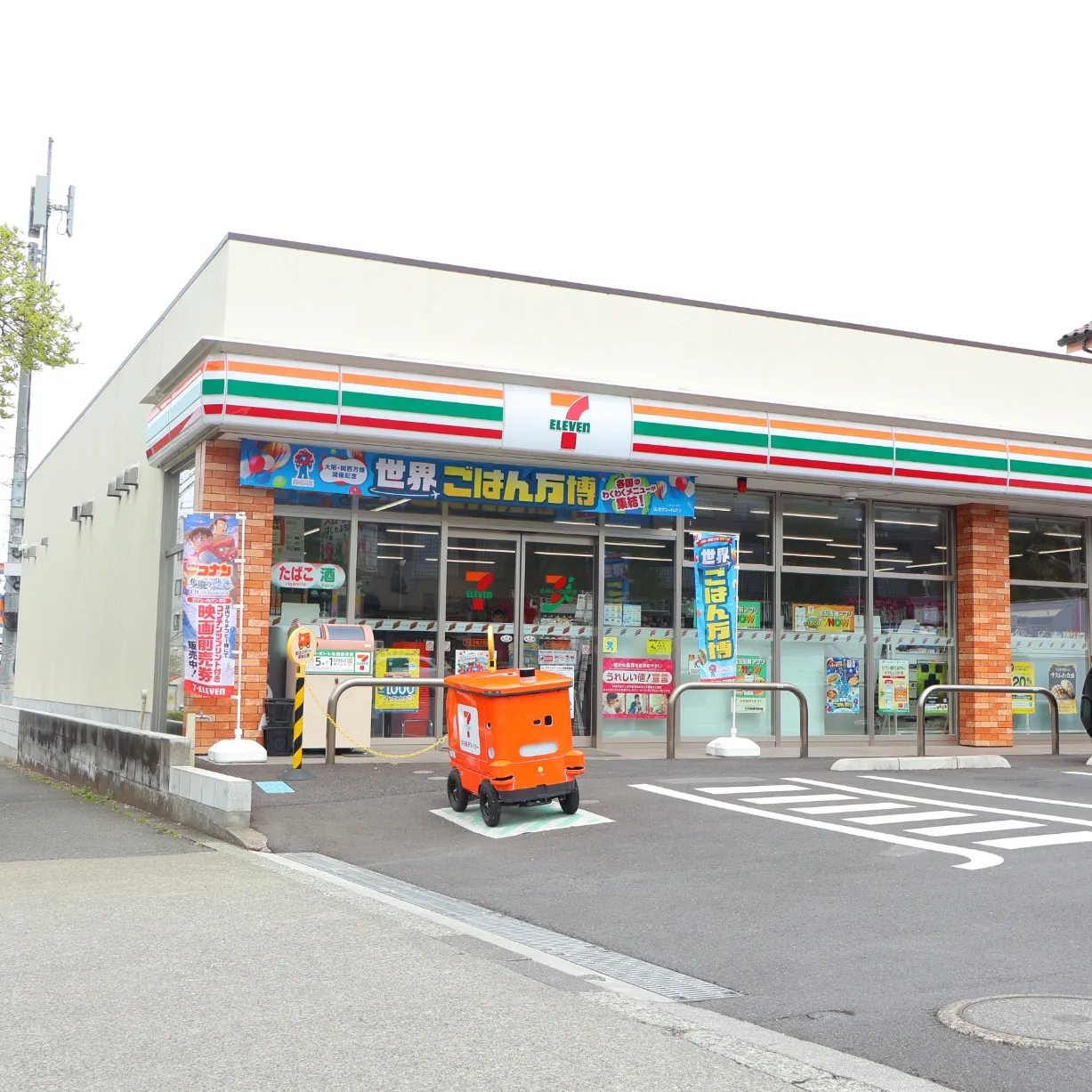
Unmanned Delivery Demonstration with 7-Eleven in Minami-Osawa
LOMBYはセブン-LOMBY conducted a real-world demonstration of unmanned delivery in collaboration with 7-Eleven in Minami-Osawa, Hachioji City.
In this trial, actual store products were delivered by autonomous delivery robots, providing valuable insights into how these machines can operate in everyday urban environments and coexist with people and traffic.
Through the experiment, we identified and addressed issues related to delivery accuracy, safety, and convenience, continuously improving the system toward full commercial deployment.
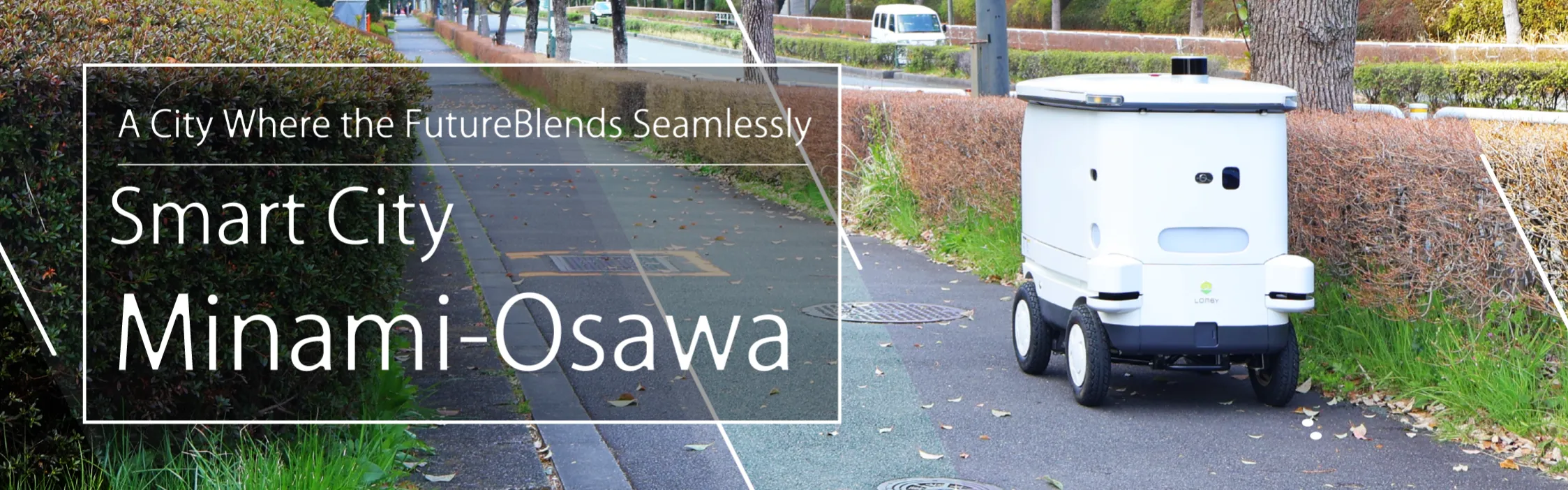
How LOMBY Works – Customer Experience Flow
STEP
1
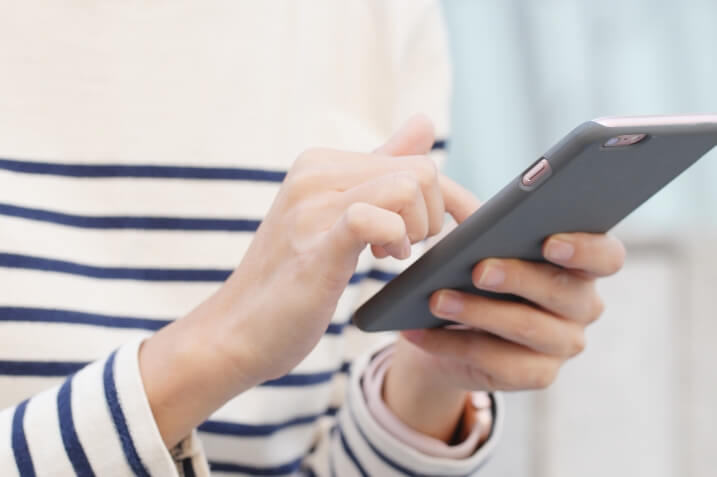
Customers purchase products through store apps
Customers use each store’s smartphone app to place an order for products.
STEP
2
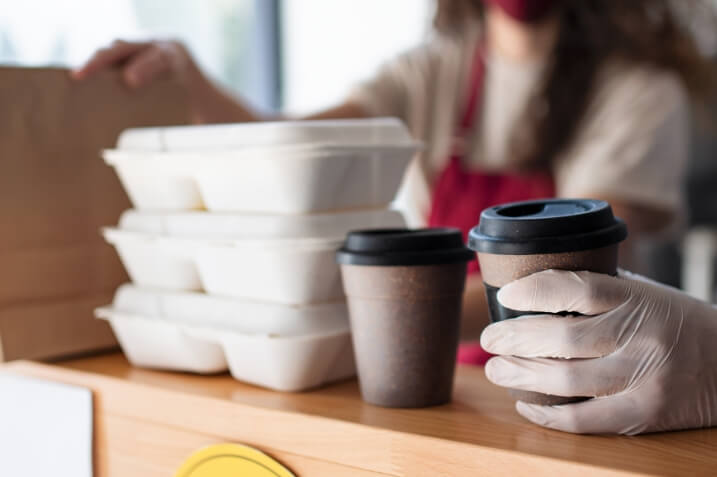
Store staff confirm orders and prepare items
Store staff check the order using a dedicated tablet app and prepare the items.
When LOMBY arrives, they scan the QR code to unlock the compartment and load the goods.
A notification is sent to the customer via a messaging app when the delivery begins.
STEP
3
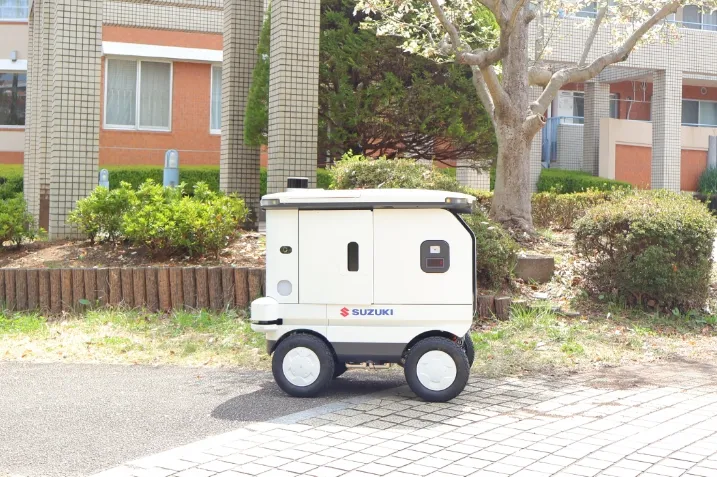
LOMBY delivers the items
LOMBY autonomously delivers the products under remote supervision.
It uses 3D maps to avoid obstacles and navigate traffic safely en route to the destination.
During delivery, the robot continuously monitors its surroundings in real-time to ensure safety.
STEP
4
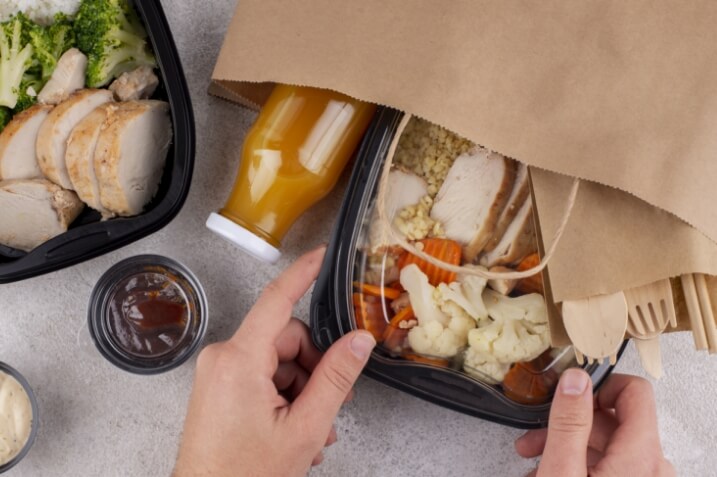
Customers receive the products from LOMBY
When LOMBY arrives at the delivery location, the customer receives a notification via the messaging app.
They scan the QR code displayed on the robot to unlock the compartment and retrieve their items.
MODEL
Model | LM-A |
---|---|
Dimensions | Length: 970 mm, Width: 638 mm, Height: 963 mm (with LiDAR), 906 mm (without LiDAR) |
Cargo Space | Front Compartment: 305 × 460 × 370 mm Rear Compartment: 365 × 460 × 370 mm |
Weight | 120kg |
Drive System | Rear-wheel direct drive |
Braking System | Regenerative braking with electromagnetic brake |
Battery | Lithium-ion battery |
Continuous Operating Time | 6km/h |
Maximum Speed (Reverse) | 3km/h |
Climbing Ability (Gradient) | 8° |
Maximum Step Height | 8㎝ |
Minimum Turning Radius | 1m |
Voice Output | VOICEVOX:Zundamon |